Table Of Content
- One of Europe’s Biggest Air Shows Featured Every Kind of Aircraft, From Drones to Business Jets
- NASA and Lockheed Martin unveil "quiet supersonic" jet
- Discover More Topics From NASA
- Astronauta de la NASA Marcos Berríos
- Uchronia founder designs own home as "love letter to French craft"
- Category:Aircraft designers

In order to succeed, it is important to properly frame your issue by identifying key design requirements. Creating a process map is the first step towards designing and building a new aircraft. Aviation’s decarbonisation relies on a mixture of incremental steps and outright technological breakthroughs. In this spirit Airbus, DLR and ONERA, two leading European research institutions, are exploring how high-performance computing can improve our understanding of the relationship between aerodynamics and aircraft efficiency.
One of Europe’s Biggest Air Shows Featured Every Kind of Aircraft, From Drones to Business Jets
A minimum clearance is required, and you can only make the landing gear so long before it weighs too much or takes up too much room when stowed. The design office at Airbus’ headquarters in Toulouse, France gathers top-level competencies such as architecture integration, general design, structural design and computation, integration tests and systems, as well as propulsion. In 2022, Delta and American Express launched the first iteration of the limited-edition Boeing Delta 747 Card design, one of the most iconic airplanes in aviation history. The new design is made with 33% metal from a retired Delta Boeing 747 plane and has a white glossy finish, which is inspired by clouds.
NASA and Lockheed Martin unveil "quiet supersonic" jet
Galpin oversees a five-year-old partnership with French aerospace lab ONERA (Office National d'Etudes et de Recherches Aérospatiales) and the German Aerospace Center DLR (Deutsches Zentrum für Luft- und Raumfahrt) on behalf of Airbus. The answer is that all these efforts are part of NASA Aeronautics’ Strategic Implementation Plan, which was developed through listening to the needs of other government agencies, industry, academia and other stakeholders in the future of aviation. To reduce greenhouse emissions – carbon dioxide being the biggest contributor – you must reduce the amount of fuel burned. To be clear, we’re not talking here about coming up with a future airliner that flies faster than sound, or a smaller personal air taxi or package delivery aircraft of the type that will be part of Advanced Air Mobility. Airbus relies on its network of regional facilities for design and engineering activities. This work is assigned to design offices and engineering centres located in Europe and extending to North America, India, and China.
Electra.aero Nabs $1.9M Army Contract for Electric Aircraft Testing - FLYING
Electra.aero Nabs $1.9M Army Contract for Electric Aircraft Testing.
Posted: Thu, 18 Apr 2024 19:54:41 GMT [source]
Discover More Topics From NASA
The goal of all these tests is to verify predicted behaviour of the systems, structure and aircraft and to demonstrate their ability to sustain conditions well exceeding what is expected during the life of the aircraft – including also all conceivable failure cases. Years of subsequent joint studies envisioned an orchestrated approach to developing advanced military rotorcraft across all “capability sets,” from light scouts to heavy lift platforms. This structured plan telegraphed to industry what the military services’ long-range plans were, so companies could keep their design, development and production teams focused on both near-term and far-term objectives. Many of those 400 engineers that have now been laid off were previously hired away from other aerospace and defense companies and may stay in the vertical flight industry.
Boeing similarly has decades of production and support contracts remaining for its CH-47 Chinook, AH-64 Apache and other military rotorcraft. Army Signal Corps bought a Wright Military Flyer from the Wright brothers for $30,000, and has kept apace for more than a century as dozens of aircraft types were converted for the armed forces. Military-technology transfer is now advancing even more rapidly into the civilian market, with the latest generation of electric aircraft currently undergoing flight testing in preparation for certification in the next few years. At first glance, private jets and military aircraft couldn’t seem further apart. But in the gray area between coddling luxury and mission-based efficiency, there’s a rich history of innovation exchange that has helped both categories stay on the bleeding edge of aviation.
NASA’s Chandra Releases Doubleheader of Blockbuster Hits
“We decided that unified controls is a proven direction to go,” he says, referring to systems that allow vertical takeoffs and landings to be executed with one hand. The advanced systems relay commands every few milliseconds via pilot input to help automate flight, the endgame being a much safer, more intuitive generation of aircraft. MachUp is a free, online aerodynamic analysis tool used for aircraft design, analysis, and optimization. This tool was developed by graduate students under the leadership of Dr. Doug Hunsaker at Utah State University. I myself have been working on the development of MachUp for over a year now.
My work specifically has related to calculating the aerodynamics of the propellers and modeling how prop-wash can affect the aerodynamics of lifting surfaces, like wings. Using this tool, aspiring aircraft designers with little to no knowledge of aerodynamics or aeronautical engineering can design their own aircraft. From a simple flying wing to a canard with distributed electronic propulsion, MachUp allows users to design their own aircraft and easily analyze its aerodynamics. During the design phase, the definition and dimensioning of all elementary parts and their interfaces are performed, and the equipment, engines and landing gear are developed by the supply chain. In the integration and qualification phases, parts are produced and assembled – both for test specimens on test benches and for the first aircraft that will serve the flight test programme. The tests are organised as a pyramid, going from lab tests at a small scale (via integration tests for checking the behaviour of complete systems) to full-scale structural tests and flight tests.
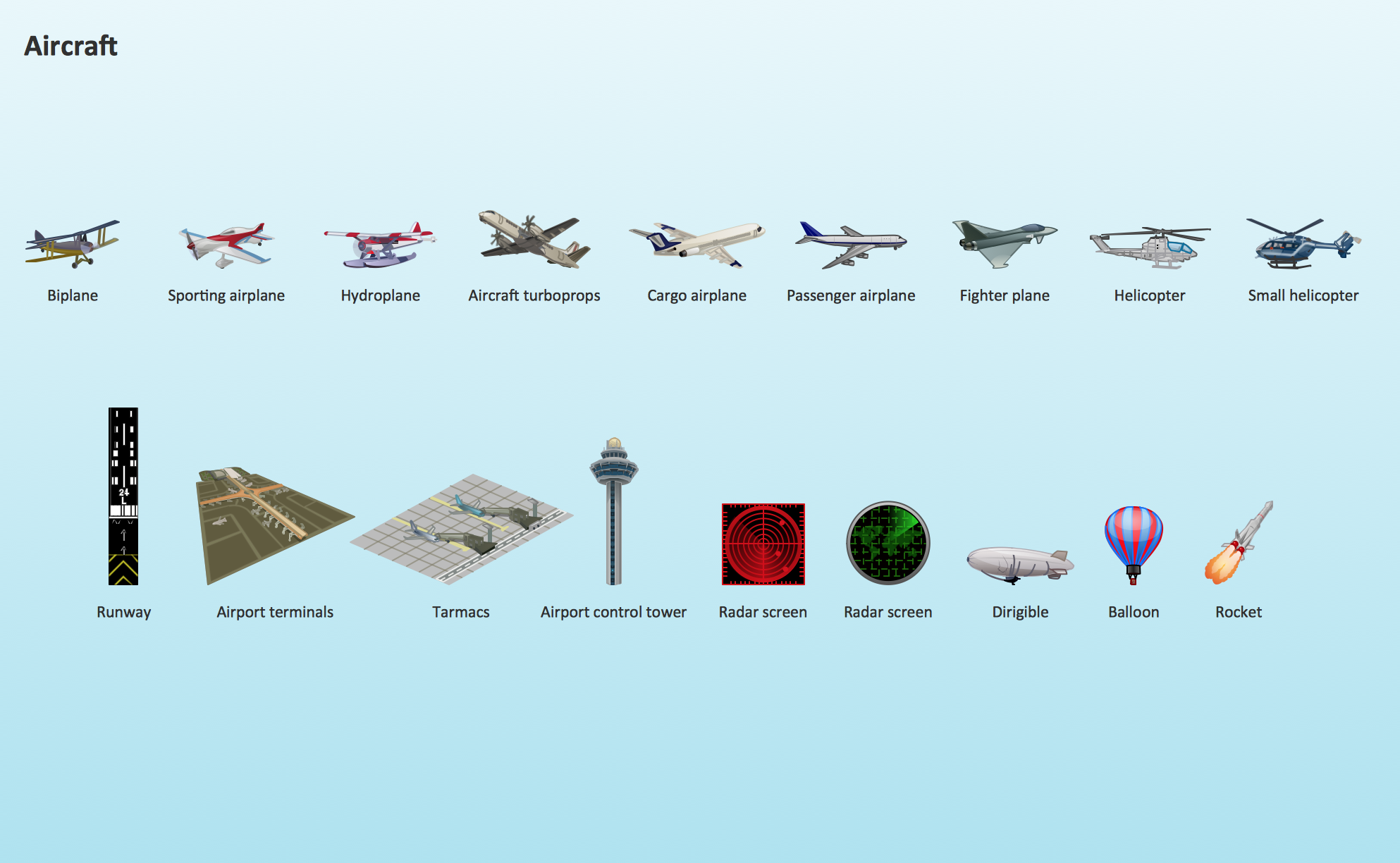
The final product is a conceptual layout of the aircraft configuration on paper or computer screen, to be reviewed by engineers and other designers. The design configuration arrived at in the conceptual design phase is then tweaked and remodeled to fit into the design parameters. In this phase, wind tunnel testing and computational fluid dynamic calculations of the flow field around the aircraft are done. Aerodynamic flaws and structural instabilities if any are corrected and the final design is drawn and finalized. The white space tackled by eVTOLs has brought with it the opportunity to invent new flight-control systems for easier, safer operation. “We’d been researching the best way to control a vehicle of this class,” explains Joby Aviation’s Peter Wilson.
When onboard pilots are not required, the diversity of practical vehicle configurations grows. Today, drones help in the study of coral reefs, high-altitude long-endurance observation and communications, and aerial photography. Future applications may include delivering packages in urban regions, medicines in remote areas, or even people, as driverless cars help pave the way for new forms of air transport.
But many others will leave, with their unique engineering expertise lost to the military rotorcraft industrial base. Future aircraft design will rely heavily on these simulations, extending their use in large-scale optimization and uncertainty quantification. A variety of computational tools is needed for conceptual design to shape optimization. These tools range from reduced-order computational models for the development of design space exploration strategies and rapid design optimization to high-fidelity computational models for trouble-shooting and performance assessment. Although the efficiency of commercial jets has improved dramatically since their introduction, the effect of airplanes on the global and local environments is significant. The Department of Defense will design, develop and field a fleet of next generation air vehicles that will ensure the United States’ dominance in the vertical lift domain throughout the 21st century and beyond.
The jet engines also can power generators to directly supply electricity to the electric motors, or to charge batteries for the electric motors to use later. This can mean an all-electric airplane in which electric motors turn propellers or fan blades to generate thrust. Such a capability could enable all sorts of new ways airplanes could be designed, either by modifying current airplanes or coming up with new configurations. It must move through the air easier, possibly use electricity to augment or power the propulsion system, and it must be as lightweight as is safely practical.
No comments:
Post a Comment